Maximising Uptime in Civil Projects: The Role of Equipment Maintenance Software
How much time—and money—are you losing to breakdowns, unplanned servicing, or idle machines?
In civil construction, downtime isn’t just frustrating—it’s expensive. When equipment fails, it can delay entire job phases, push out delivery milestones, and trigger costly contract penalties. But here’s the good news: with the right maintenance strategy, much of this risk is preventable.
This blog explores how equipment maintenance software can transform your uptime strategy. From scheduled maintenance based on usage or hours to real-time tracking of machine health and availability, we’ll show how digital tools keep your civil sites running smoothly.
Understanding Equipment Maintenance in Civil Construction
Equipment maintenance refers to the processes and tools used to keep machinery, vehicles, and plant in safe working order. In civil construction, this includes excavators, graders, rollers, loaders, and fleet vehicles—assets essential to daily operations.
Traditional maintenance methods—spreadsheets, clipboards, and reactive servicing—don’t cut it anymore. The cost of a single machine failure can exceed $5,000 per day, especially when it disrupts concrete pours or earthmoving schedules.
That’s why forward-thinking contractors are turning to platforms like Kynection’s Asset & Equipment Maintenance module. It digitises the entire maintenance lifecycle, connecting it with scheduling, job progress, and site activity for better control.
According to a 2023 report by the Australian Industry Standards Committee, predictive maintenance technologies are projected to reduce unplanned downtime by up to 30% in construction and mining over the next five years (source).
What It Looks Like in Practice
Let’s say your grader is scheduled for a roadworks job on Monday.
With Kynection’s Scheduler, it’s already been allocated to the project. But behind the scenes, the system checks the asset’s usage logs and flags that it’s due for servicing based on operating hours.
An automated notification goes out to your maintenance team. They complete the service using a digital form and close the job in the system. The grader’s maintenance history is updated in real time, and the Scheduler is automatically notified that the asset is cleared and ready to go.
The result? Downtime prevented, compliance maintained, and site coordination uninterrupted.
Meanwhile, site supervisors use the Job Management module to track plant performance from their mobile device—ensuring machines are on-task and operational from the field.
Key Components of a Smart Maintenance Workflow
🔄 Scheduled Maintenance Based on Usage or Hours
With Kynection’s Asset Maintenance tools, you can automate servicing schedules based on real-time data:
- Hours logged: Trigger servicing after X operating hours
- Job assignment: Schedule maintenance after project completion
- Calendar cycles: Set weekly/monthly/annual servicing routines
This removes guesswork and keeps assets compliant with regulatory servicing intervals.
🛠️ Prevent Downtime Across Multiple Civil Sites
The Scheduler module offers visibility over resource availability across all sites. You can:
- See which machines are booked, serviced, or awaiting repair
- Reschedule assets quickly in the event of faults
- Avoid assigning machines that are out of service or unsafe
🧭 Assign Machines to Specific Projects or Stages
Through Project Management, equipment can be assigned to project stages and milestones—ensuring it’s where it needs to be, when it needs to be.
- Allocate machines to excavation, drainage, or handover phases
- Link usage logs and servicing to project budgets
- Get insights on actual vs. planned asset usage
📲 Track Plant Performance from Your Mobile Device
Using Kynection’s Job Management, field workers and supervisors can:
- View active machine assignments
- Report faults or hazards instantly
- Access manuals, servicing records, and logs
Mobile access ensures that no issue goes unnoticed—keeping machines operational and safe.
Strategic Use Cases for Civil Contractors
🧾 Compliance and Audit Readiness
Plant breakdowns often trigger regulatory investigations—especially when safety is compromised. With full digital servicing logs and photo attachments, you can prove maintenance was conducted and documented.
This level of record-keeping aligns with heavy vehicle and plant safety regulations outlined by Safe Work Australia (Safe Work Australia).
🔄 Fleet Resource Allocation
Got a grader sitting idle at Site A while Site B is behind schedule? With real-time scheduling and visibility, you can move assets fluidly—maximising utilisation.
This is especially useful for contractors managing large civil fleets across highways, subdivisions, and rail projects.
🧠 Predictive Insights and Downtime Trends
Using analytics, contractors can identify:
- Machines with higher breakdown frequency
- Peak downtime periods by site or job type
- Cost trends associated with specific assets
This data supports better decision-making on repairs, replacement, or leasing.
Planning for Successful Implementation
Before rolling out equipment maintenance software:
- Create an asset register – Record all machines with ID tags
- Standardise your servicing types – Set preventive and corrective schedules
- Train users in the field – Keep logging simple with mobile-first workflows
- Assign maintenance roles – Who logs, who signs off, and who services?
- Integrate with job and scheduling tools – Ensure site-level visibility
Future Trends in Equipment Maintenance
The future is looking smarter, more connected, and more proactive:
- IoT sensors are enabling real-time fault detection
- AI maintenance algorithms are predicting failures before they happen
- 5G connectivity allows constant updates from remote machines
- Green fleet tracking is helping firms reduce emissions and fuel use
Contractors who embrace predictive maintenance will benefit from fewer breakdowns, safer operations, and stronger margins.
Optimisation Tips to Keep Uptime High
Problem |
Solution |
Missed servicing dates |
Set automated alerts based on hours or job triggers |
Unclear asset availability |
Use Scheduler to track machines across sites |
Unreported machine issues |
Enable mobile fault reporting for crews |
Paper-based maintenance logs |
Move to eForms with digital audit trails |
Continuous improvement isn’t just about tech—it’s about the habits that support it.
Action Plan: Uptime Starts with a Smarter System
Phase 1: Foundation (Month 1–2)
- Build your digital asset register
- Roll out mobile eForms for servicing
- Train mechanics and operators
Phase 2: Expansion (Month 3–6)
- Integrate maintenance with job scheduling
- Track downtime events and causes
- Automate reminders for inspections
Phase 3: Optimisation (Month 6+)
- Use downtime reports for capital decisions
- Add predictive triggers (sensor-based)
- Link asset performance to project profitability
By phase 3, you’ll not only be preventing downtime—you’ll be using machine data to improve project outcomes.
FAQs
What is equipment maintenance software?
It’s a digital tool used to track, schedule, and manage servicing, repairs, and inspections of plant and machinery across job sites.
Can I track servicing history for each machine?
Yes. Each asset has a digital logbook with servicing dates, parts replaced, faults, and more—great for audits or resale value.
Does it work for mobile field teams?
Absolutely. Field crews can log faults, complete checks, and view asset data from mobile devices—even offline.
How does this reduce downtime?
By using servicing alerts, real-time visibility, and proactive tracking, teams can prevent unplanned breakdowns and reschedule faster.
Can it connect to our scheduling and job tools?
Yes. Kynection’s system links Scheduler, Project Management, and Job Management modules to give full visibility.
Tired of losing time (and money) to preventable breakdowns? Discover how Kynection’s Asset & Equipment Maintenance tools can help your team maximise uptime across every civil job site.
You May Also Like
These Related Stories
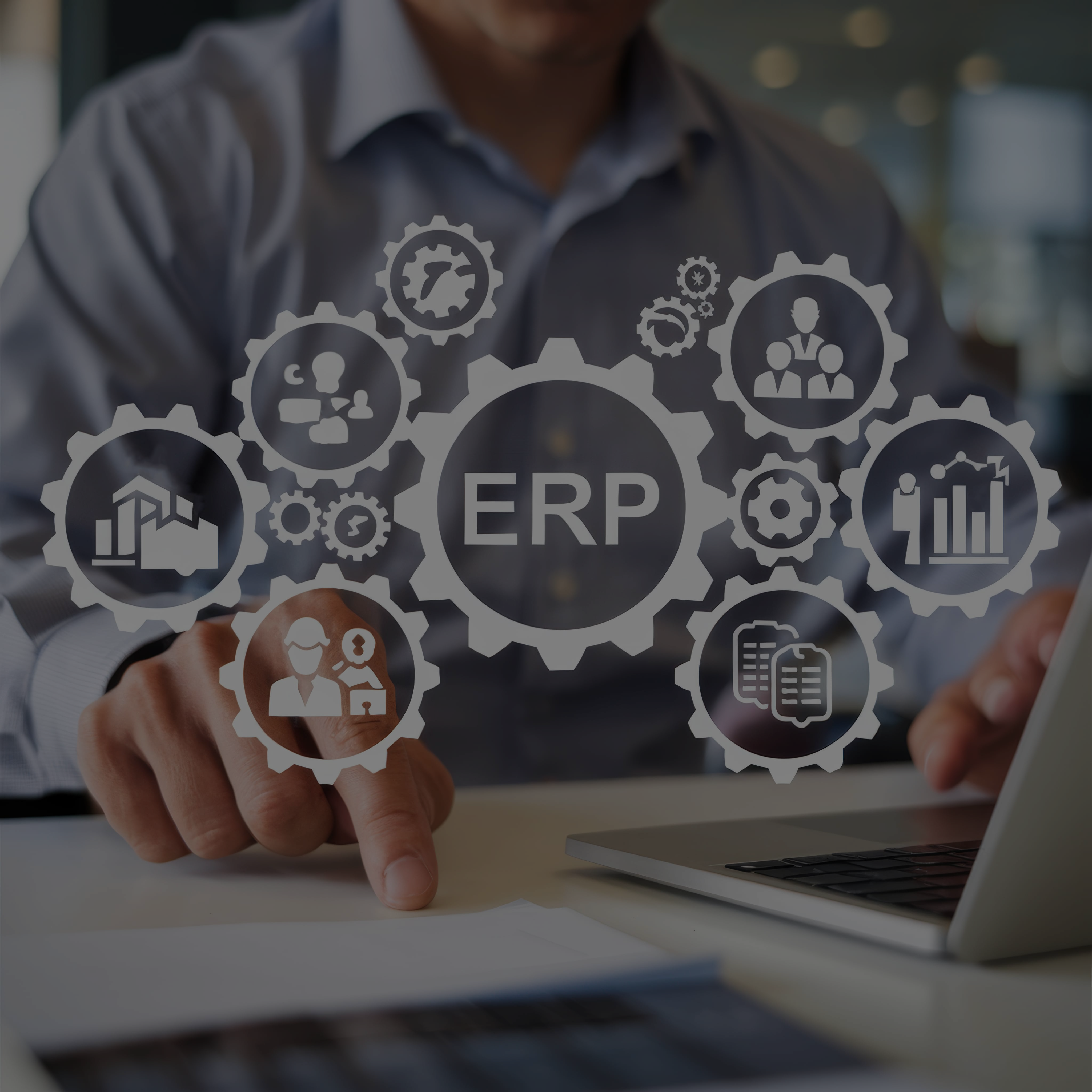
Civil Construction Meets The Cloud Acumatica Integration For Seamless Project Accounting
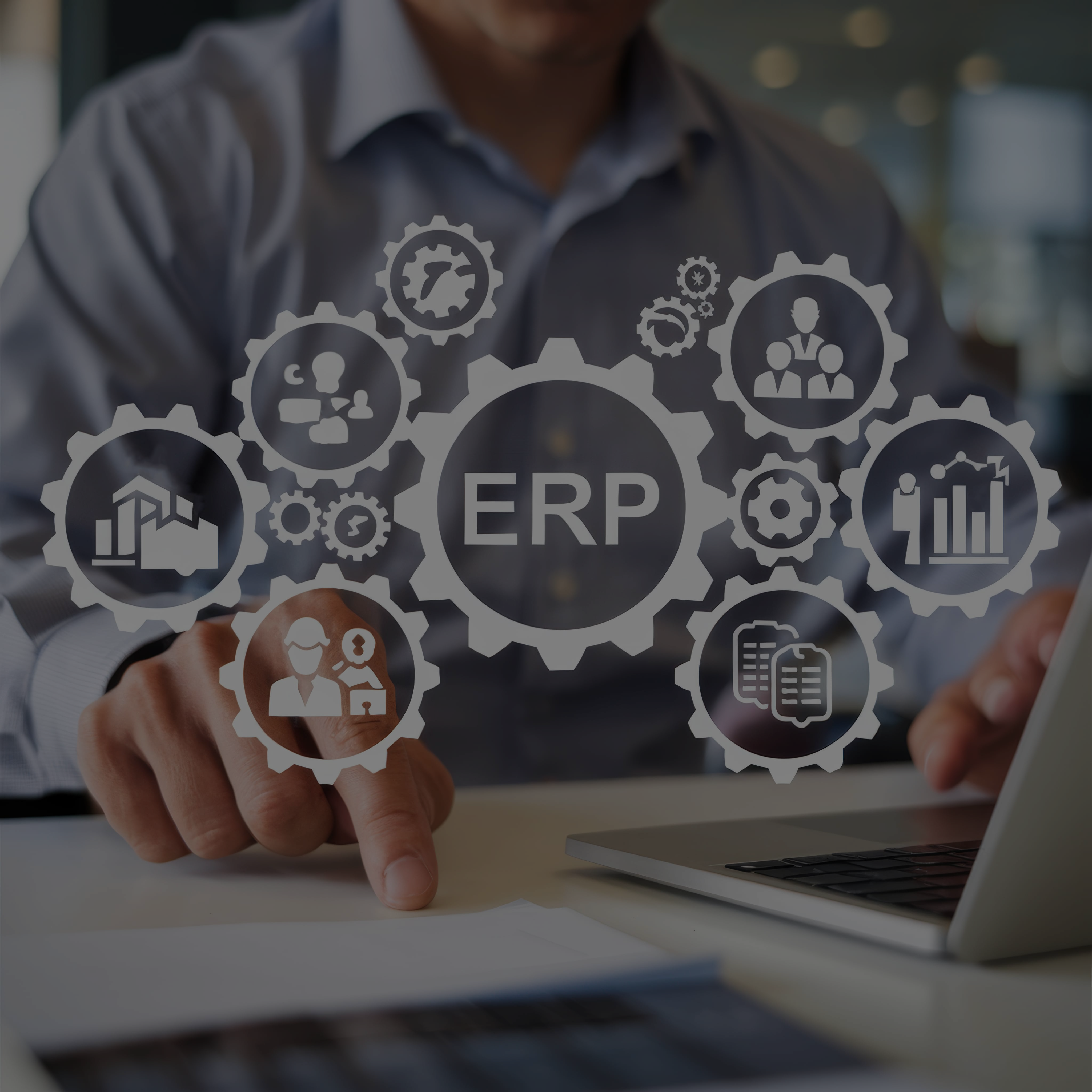
From Dirt to Data: How Civil Contractors Are Going Digital with Smart Site Management

No Comments Yet
Let us know what you think